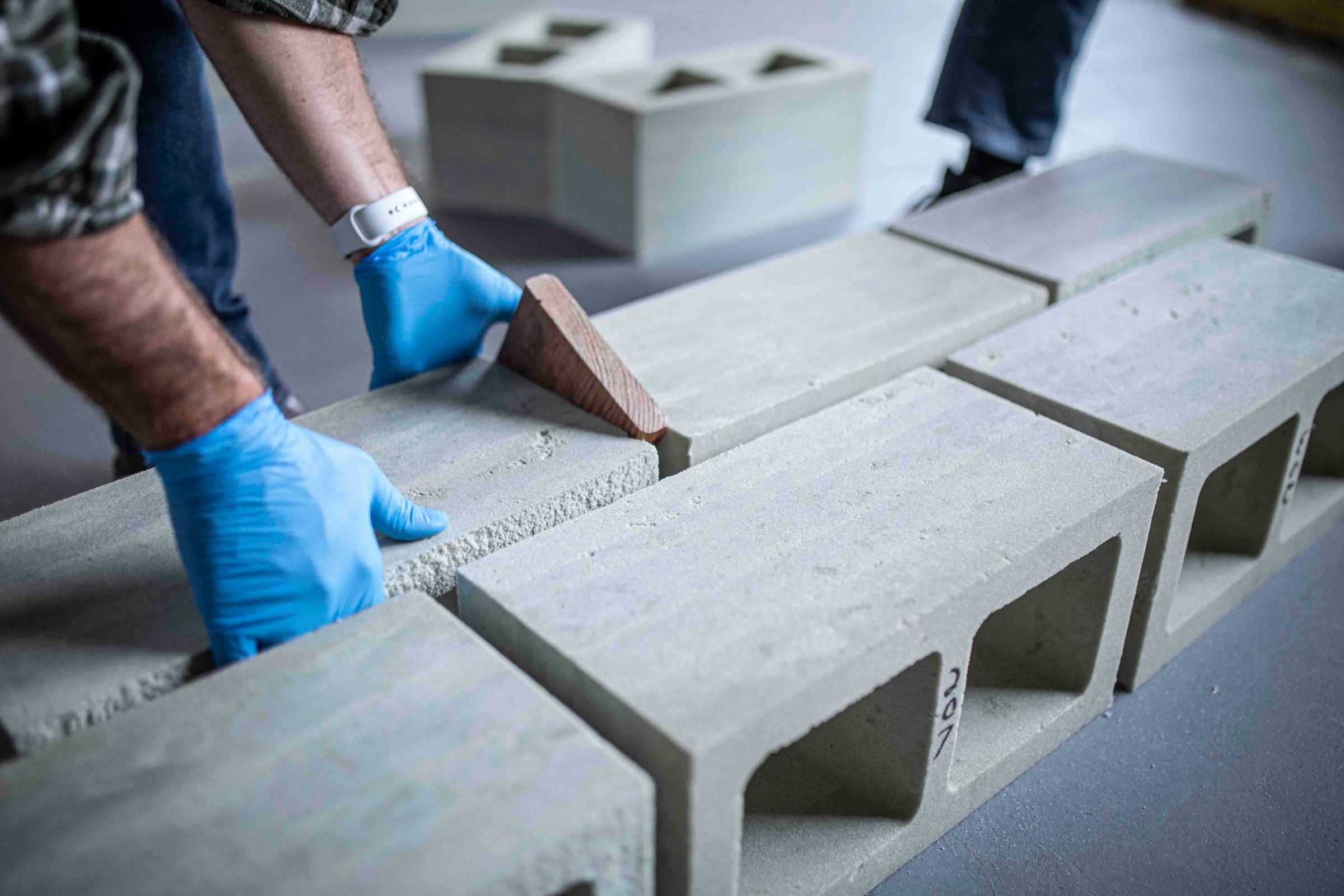
Cement—the essential binding ingredient in concrete, bricks, and mortar—is a climate nightmare. To make it, you heat limestone and clay to extremely high temperatures using carbon-polluting fossil fuels. That triggers a chemical process, which also releases huge amounts of carbon dioxide into the atmosphere. The process is so carbon-intensive and cement is so widely-used that it accounts for around 8% of global CO2 emissions. With the world’s building stock projected to double by 2060, climate advocates are desperate for alternative materials to come to market—fast.
A factory in Longmont, Colo., may have the answer. By the end of this year, it will begin churning out concrete bricks made not from cement—but from algae. Prometheus Materials, which formed in 2021 out of a research project at the University of Colorado, takes microalgae normally found in lakes or ponds and grows it in bioreactors. They add air, so the algae can feed on the carbon dioxide it contains, as well as sea water and light from LED lamps. That allows the algae to produce a cement-like substance capable of bonding together sand with gravel or stone to make concrete. The method mimics the natural process through which organisms form hard coral reefs and seashells.
The algae-based bricks are set to be commercially available in 2023. They were designed in partnership with and part-funded by U.S. architecture firm Skidmore, Owings & Merrill (SOM)—known for creating the Burj Khalifa in Dubai and New York’s One World Trade Center.
Making the bricks currently emits a tenth of the CO2 of conventional concrete block production, according to Prometheus Materials CEO Loren Burnett. When the company finishes installing solar panels to power its manufacturing plant, that process will be carbon neutral, and, in three years, carbon negative, according to Burnett. “There’s virtually no CO2 emitted during the process and we actually sequester CO2,” he says. “Because the algae absorbs it through photosynthesis, and we then embed that algae into our building materials.”
Prometheus’ production timeline puts it near the forefront of a movement to replace carbon-intensive conventional building materials, like steel and concrete, with materials derived from plants and other organisms. The so-called “bio-based” materials sector is still in its infancy. But supporters say it has the potential to transform the construction industry from one of the world’s biggest emitters—responsible for 11% of CO2 emissions—to an absorber of carbon. That is, from a climate villain, to part of the solution.
A new era of plant-based buildings
Using nature in construction is nothing new. People have been taking the plants and organic matter that grow around them and turning it into structures for thousands of years. From South Africa to England to Afghanistan, straw has long been mixed with soil and water to make cob. Fast-growing and strong bamboo is a key element of a lot of traditional architecture in East Asia. And timber has retained its historic popularity in many countries, with 90% of new homes in the U.S. still made with wood frames. Over the last few decades, environmental campaigners have pushed for those carbon-absorbing materials to become the norm in homes and small-scale construction.

But building on a large scale with natural materials has proved difficult (though a few high-profile wooden skyscrapers are popping up in some cities). So, scientists are developing a new generation of organic-derived materials strong and versatile enough to replace carbon-intensive steel and concrete. To stimulate those efforts, in June, the U.S. Department of Energy announced $39 million in grants for 18 projects working on “technologies that can transform buildings into net carbon storage structures.” The University of Colorado team behind the algae bricks is one of the recipients. Another grantee is working on a fungi-based insulation material that can be used to retrofit homes. A third wants to add microbes to wood to create a “living” material “with the strength of steel.”
Read more: Homes Made from Straw or Fungi Can Now Get You a Cheaper Mortgage in the Netherlands
Only a handful of new bio-based materials have made it to market already: bioMason, a Durham, N.C.-based company, which feeds bacteria with calcium and CO2 to generate a bio-cement, currently sells tiles in the U.S. and Europe. Meanwhile, Dutch biotech company Basilisk sells concrete containing limestone-producing bacteria, as well as a mixture that can be applied to existing buildings, which allows concrete to self-heal from cracks, reducing the need for unnecessary demolitions and re-builds.
Most companies developing bio-based materials face the same challenges as other climate-friendly tech: they are still struggling to scale up lab successes to a commercial scale, at costs that can compete with carbon-polluting alternatives. Some also need to figure out how to obtain large volumes of their chosen organic matter without competing for land with the agriculture industry, nature restoration projects, and renewable energy.
What would it take for algae bricks to go mainstream?
But Brant Coletta, a partner at SOM, who worked with Prometheus to design their bricks, claims the technology’s “easy scalability” was the main draw for the architecture firm. Initially Prometheus will grow its algae—which can double in volume every four to six hours—at its Colorado plant, to produce its cement-like material, turn it into bricks, and ship them to customers. Within 18 months, they will start shipping a dried, light-weight version of the bio-cement, so that customers can turn it into bricks—without expensive equipment or highly trained staff.

To convince Coletta of that last point, one of Prometheus’ co-founders sent him a few bricks in the mail along with photos of his young children making them in their backyard. “Quality control probably wasn’t the strongest in that, but it demonstrates how this is a product that can find its way into the global market,” Coletta says.
Safety certification of Prometheus’ algae bricks, by the American Society for Testing and Materials, should be complete by the end of the year, along with construction of the manufacturing plant, according to Burnett. He says the plant will immediately begin producing “tens of thousands” of bricks and quickly scale up to a “significant” amount—though he would not disclose projected volumes, citing commercial reasons. Burnett also declined to share the final price of the bricks before production begins and the company can be sure of its costs. “Our goal is to not have any green premium attached to our blocks,” he says.
Even if the cost of the bricks proves to be comparable to conventional concrete blocks, it may take architects and developers a few years to trust that “they will perform and have limited-to-no cost impact on projects,” Coletta says. There’s not much data on how prevalent organic-derived materials are in the construction industry. Even in the Netherlands, which has emerged as a hub of sustainable building practices in recent years, experts say around 3% of materials used are bio-based.
But SOM, which styles itself as a leader in green architecture and is keen to provide clients with low-carbon options, will add the bricks to its roster of materials as soon as safety certification is complete. “We’ve had clients come in and they see us working on this and say they want it in their project right away,” Coletta says. “It’s hard for me to hold my design teams back.”
More Must-Reads from TIME
- Cybersecurity Experts Are Sounding the Alarm on DOGE
- Meet the 2025 Women of the Year
- The Harsh Truth About Disability Inclusion
- Why Do More Young Adults Have Cancer?
- Colman Domingo Leads With Radical Love
- How to Get Better at Doing Things Alone
- Michelle Zauner Stares Down the Darkness
Write to Ciara Nugent at ciara.nugent@time.com