Jani, a 4-foot plush giraffe, arrived on my doorstep in mid-July, her neck bent backwards so that she could fit in the FedEx box, her brown eyes glassy, as if still finding her bearings after a long journey at sea.
What a journey it had been. Viahart, the company that sells Jani on Amazon, had ordered a container’s worth of plush toys including her in August of last year. This was around the time that U.S. consumers, cooped up at home, started spending again after an initial dip in the beginning of the pandemic. And as the demand for toys and TVs and couches rose, the ships and trains and trucks carrying them got overwhelmed and added hefty congestion surcharges. That made it much more expensive to get Jani to my doorstep.
“Good Day, No rail schedule yet. Rail delays due to chassis shortage & port congestion. Please continue to monitor,” reads an email from COSCO Shipping NA, the company responsible for getting the container from China to Viahart’s Texas warehouse, about why the container was sitting in the port of LA for weeks and weeks. Viahart now pays around $21,000 to send a 40-foot container from China to Texas, up from $4,700 before the pandemic.
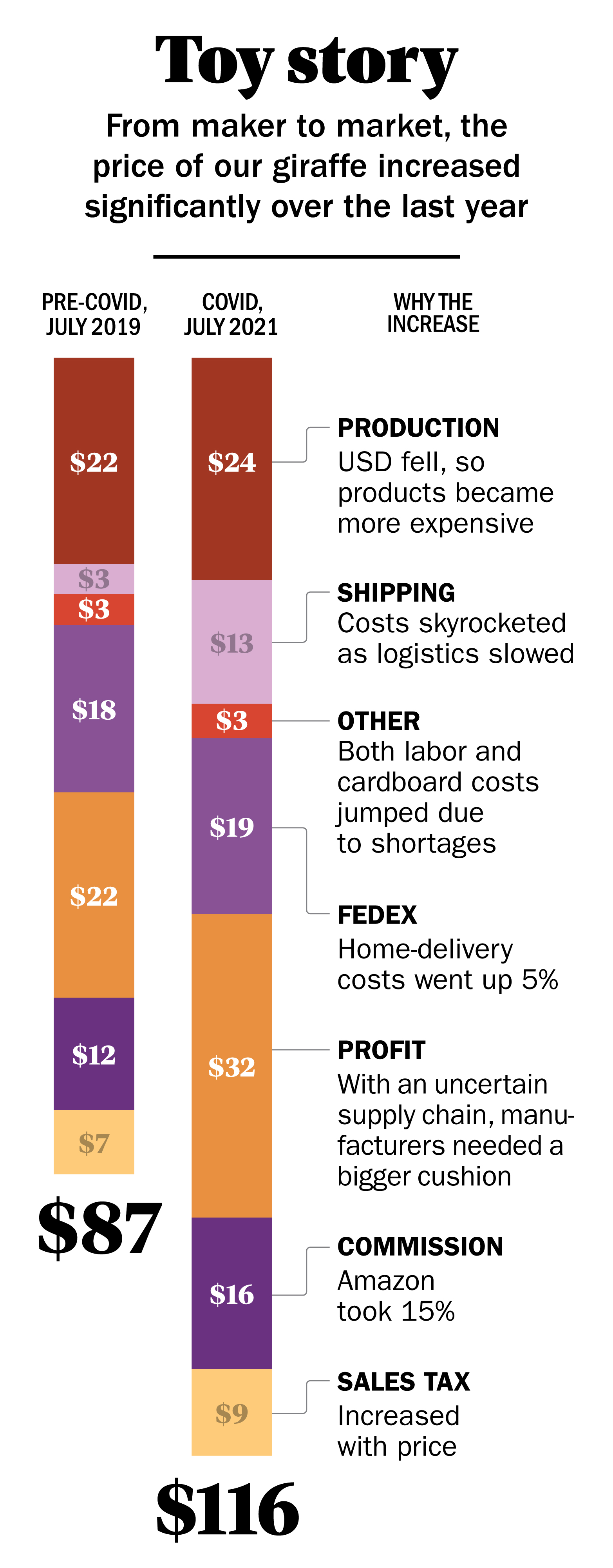
There’s no question that the U.S. economy is experiencing a surge in inflation. The cost of goods was up 5.4% in July from the same period a year ago, the largest annual increase since 2008. Inflation can be caused by many things—increased consumer demand, a rise in wages, a spike in other costs. This time around, economists agree that inflation is being caused by an overwhelmed logistics network. “If you look at where prices are rising, it’s not across the board, it’s in really specific sectors” like lumber and cars, says J.W. Mason, an economics professor at John Jay College. These sectors can’t produce things as quickly as consumers want them for a variety of reasons, he says—”It’s about those specific glitches that come from reopening.”
These rising prices are stressful for consumers, whose money doesn’t go as far as it used to, and for companies, who are seeing their costs rise and have no choice but to pass it on to consumers. When the cost of getting a container full of stuffed toys quadruples, “we have to raise prices in order to make money,” says Mike Molson Hart, the president of Viahart, which sells plush animals and toys called Brain Flakes, primarily on Amazon. “The question becomes, is anyone going to buy this at the new, higher price? We’re flying blind.”
If you want to understand what’s driving inflation in the U.S. economy right now, look no further than Jani the giraffe. Jani used to cost around $87. Now she’s around $116, as costs went up on every step of her journey.
‘A war being waged’ over container ships
Jani was made in China, in a factory about four hours from the port of Qingdao, which is about halfway between Beijing and Shanghai. Viahart sent detailed specifications to the factory, where bags of white stuffed tigers, orange tiger tails, and giraffes like Jani lie askew on tables. The company placed an order for a 40-foot container full of giraffes, tigers, dragons and other stuffed animals on August 18 of last year.
Though some products have gotten more expensive to make because of the rising cost of raw materials like glass and metal, Viahart didn’t have to pay much more to make Jani. Stuffed animals are made from plastic pellets, which are made from oil, but when Jani was made in August, oil prices were at historic lows because demand had collapsed. Before the pandemic, Jani cost about $22.04 to make; in August she cost $23.76 because the value of the U.S. dollar had fallen in comparison to China’s RMB.
But getting Jani to the U.S. was much more expensive than it used to be. Viahart knew it needed to hire a shipping company to get the sealed container from the factory in China to its warehouse in Texas, but because it’s a small company, it doesn’t negotiate with shipping companies directly. Instead, it called a freight forwarder—essentially a logistics company that negotiates the best prices for shipping a single container, rather than a whole boatload of goods.

Beginning around April of 2020, even the freight forwarders, who do this professionally, started having a hard time finding space on ships. In normal years, demand for space on ships peaks around Chinese New Year, right before all the factories in China shut down for the holiday, says Jeffrey Wang, business development executive at Air Tiger Express, a freight forwarder Viahart frequently uses. Then there’s a lull. In 2020, there was no lull. People started ordering things, but factories in China were closed because of COVID-19. When they reopened, there weren’t enough containers to hold all the goods, nor was there enough ship space.
Knowing that space on ships was in demand, shipping companies started raising prices, sometimes forcing companies into bidding wars to nab limited spots on ships. “Right now, it’s kind of the wild, wild West—everyone is desperate for cargo space,” Wang says.
The factory finished making Jani and the other plush toys on September 27, about 40 days after Viahart placed the order. On October 7, a container of plush toys left the factory by truck and was loaded on a vessel from the COSCO shipping line, the CSCL Winter.
If she had stayed on that boat, she would have arrived in the U.S. on November 4, after the ship stopped in British Columbia and then the Port of Long Beach, which, together with the adjoining Port of Los Angeles, is the busiest container port in the United States. But Jani and her container were offloaded in Shanghai.

Viahart got no explanation for why it was offloaded; the company was just informed that the container would now arrive on November 11, rather than the previous week. “Where is the container now?” Sarah Joy Tan, Viahart’s exceedingly patient production and quality manager wrote, in an email, to the freight forwarder. “I didn’t expect it to be more than 2 weeks in Shanghai.” The forwarder wrote back, “container will be rolled to another mother vessel,” without any other information.
Finally, on October 26, Jani was loaded onto another ship in Shanghai, the Judith Schulte. It made stops in three other ports in China before chugging across the Pacific on its way to the Port of Los Angeles.
“There is a war being waged in container terminals around the world,” says Sebastien Breteau, the CEO of QIMA, which does quality control along the supply chain. Freight forwarders and shippers are fighting one another to get shipping slots.
Jani’s journey from the factory to the port, which took about 38 days before the pandemic, took 53 last fall. For that slower service, Viahart paid about $13.27 per stuffed animal for shipping, up from $3.01 before the pandemic.
Congestion at the ports
As the Judith Schulte approached the port of Los Angeles, dozens of other container ships were bringing goods from Asia, too. The flow of ships had slowed dramatically in the first six months of 2020, after some factories closed because of COVID-19 and American consumers waited to see what was going to happen. Then, in the summer, shipping volumes started climbing again. The number of TEUs—essentially 20-feet containers—arriving in the Port of Los Angeles in October reached nearly 511,000 in October, up from 400,000 in October 2019, and double what it was in March.
But that spike in traffic after such a lull caused congestion, and the ports couldn’t handle all the ships like the Judith Schulte coming in to unload goods. Before the pandemic, it was unusual to see one vessel waiting at anchor off the ports; by the beginning of 2021, there were around 40 ships anchored and waiting to unload. That bottleneck has been clogged again lately, with 37 ships waiting offshore the ports of Los Angeles and Long Beach as of Sunday.
The Judith Schulte did not have to wait offshore, but she did slow down halfway across the Pacific, from an average of 22 knots to 20, according to Spire, which uses satellites to provide data for the maritime industry. The ship was supposed to arrive on November 11, but did not get to a container terminal at the Port of Los Angeles until November 16. Then, it sat for seven days before it left, which is an “exceptionally long time,” according to Spire. Jani’s container was offloaded on November 19. She was not put on a train until December 20.
“Can you please check if we already have a schedule to load the container on the rail?” Joy Tan wrote, to the freight forwarder, on December 3, after many emails asking why the container had not moved. He wrote back: “As previously advised, container is still at the terminal. it’s Cosco’s responsibility to set up containers for rail move and Cosco’s response was ‘…container is still at the terminal. Please continue to monitor …’ We really are trying to get some updates, but we are at the mercy of the carrier here.”
The quiet frustration of the emails from Viahart, who were powerless to do anything to move its container, is one reason why Jeffrey Wang now tells his customers that containers are arriving two weeks later than the carrier said they would. Before the pandemic, he would just pad the date by a few days.
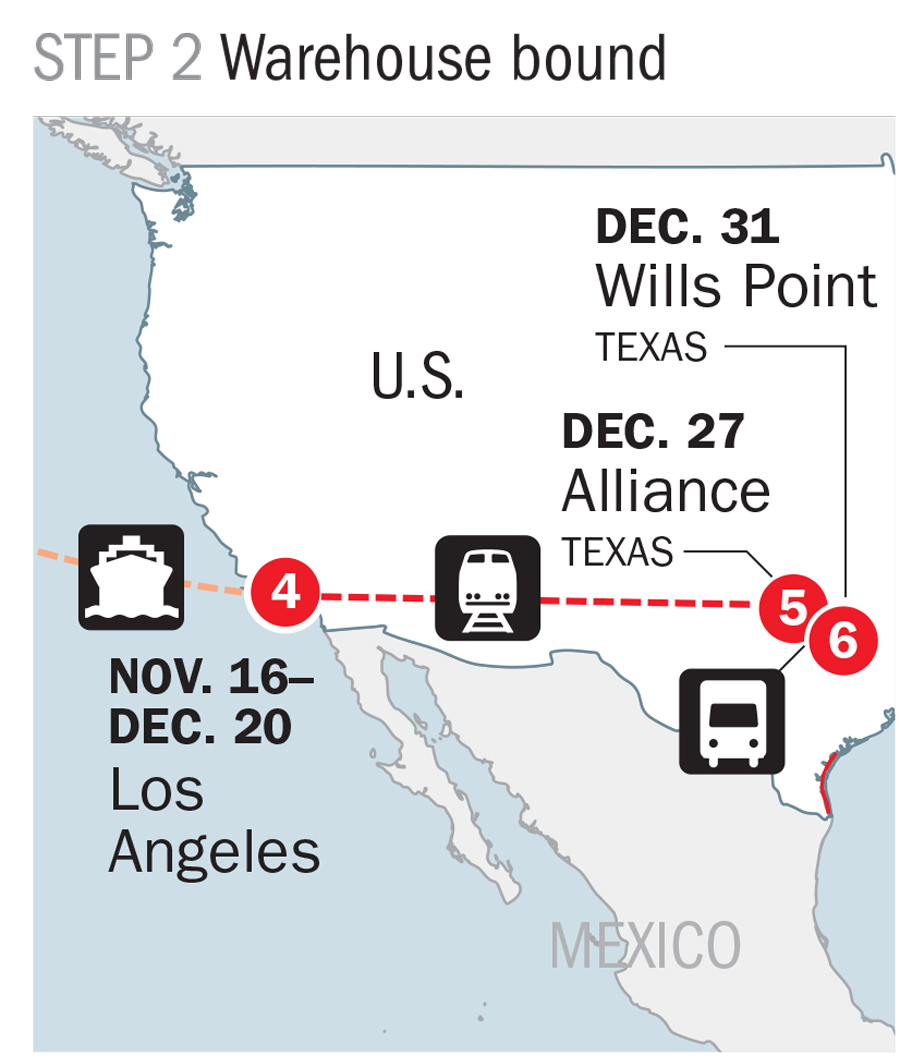
I tried to get an answer for why Jani’s container was delayed in Shanghai, why the boat was so late and took so long to get unloaded, and why the container sat in the port of Los Angeles for more than a month. But every operator in the supply chain blamed someone else.
Mike Molson Hart, the president of Viahart, attributed the delays to the fact that the U.S. ports don’t run 24/7, as ports in Asia do. But Mario Cordero, the executive director of the Port of Long Beach, says the ports can’t run 24/7 until the truckers who pick up containers and the warehouses that unload them also operate 24/7. Truckers say they can’t get the chassis needed to transport containers from ports and trains to warehouses because the shipping companies are holding them hostage to make money from the truckers they have special deals with, according to a lawsuit filed by the American Trucking Association. COSCO, the shipping company that moved Jani, in turn blamed “port congestion,” saying containers that were unloaded weeks ago cannot be reached, and said there was a lack of rail chassis to move the goods.
The “dwell time,” essentially the amount of time a container is sitting onshore before being loaded onto trucks, at the Ports of Los Angeles and Long Beach, was 4.76 days in June, up from two days in March of 2020, according to the Pacific Merchant Shipping Association. Containers sat even longer before getting on trains—an average of 11.8 days, up from 7.9 days in January, when the association started measuring. Nearly one-quarter of containers sit for more than five days before getting picked up. Operating 24/7 might not change anything, says Jessica Alvarenga, manager of government affairs at the Pacific Merchant Shipping Association—when shipping companies post nighttime appointments for trucks to pick up cargo, they aren’t being filled.
A train and trucking shortage
Cordero says there aren’t enough railcars to transport containers from the ports of Los Angeles and Long Beach, but BNSF, the railroad that eventually moved Jani’s container, blames high dwell time at inland facilities where the containers can’t be unloaded quickly enough. “While we operate 24/7, certain parts of the supply chain do not, creating additional challenges to meet this unprecedented demand,” the railroad said, in a statement. Carlos Ramirez, a terminal operator who dispatches trucks to pick up containers from inland facilities, says his truckers have issues delivering containers to warehouses because they’re so short on staff. “We’ve had containers sit for a week or two in our yard because they don’t have the manpower to unload it,” he says. His company hires owner operators who have their own trucks but it’s gotten more difficult to find any to hire in the last year, he says.
In short, it’s everybody’s fault, and nobody’s too. “Because the volume surge has affected every part of the supply chain, however, there is no single set of actors – ocean carriers, rail carriers, truckers, marine terminals, or cargo owner warehouses and distribution centers – that can clear the bottlenecks singlehandedly,” John W. Butler, president and CEO of the World Shipping Council, a lobbying group for liner ships, testified at a June Congressional hearing about supply chain delays.
All of this meant that it took 40 days for Jani to get to Viahart’s Texas warehouse after she was unloaded from the ship, even though she could have walked in about half that time, were she a real giraffe. She arrived at the warehouse on December 29, although Viahart had initially been told it would arrive more than a month earlier.
Along the way, as delays mount, every company along the supply chain is raising prices. BNSF has started charging for chassis and containers sitting too long in its facilities. COSCO and other shipping companies raised rates and started charging congestion fees. Ramirez raised prices for container storage in his yard, and will soon increase the rate he pays drivers to improve retention. Wages for truckers and warehouse workers have jumped 8% since 2019, after growing at a rate of 4% for the two years before that.
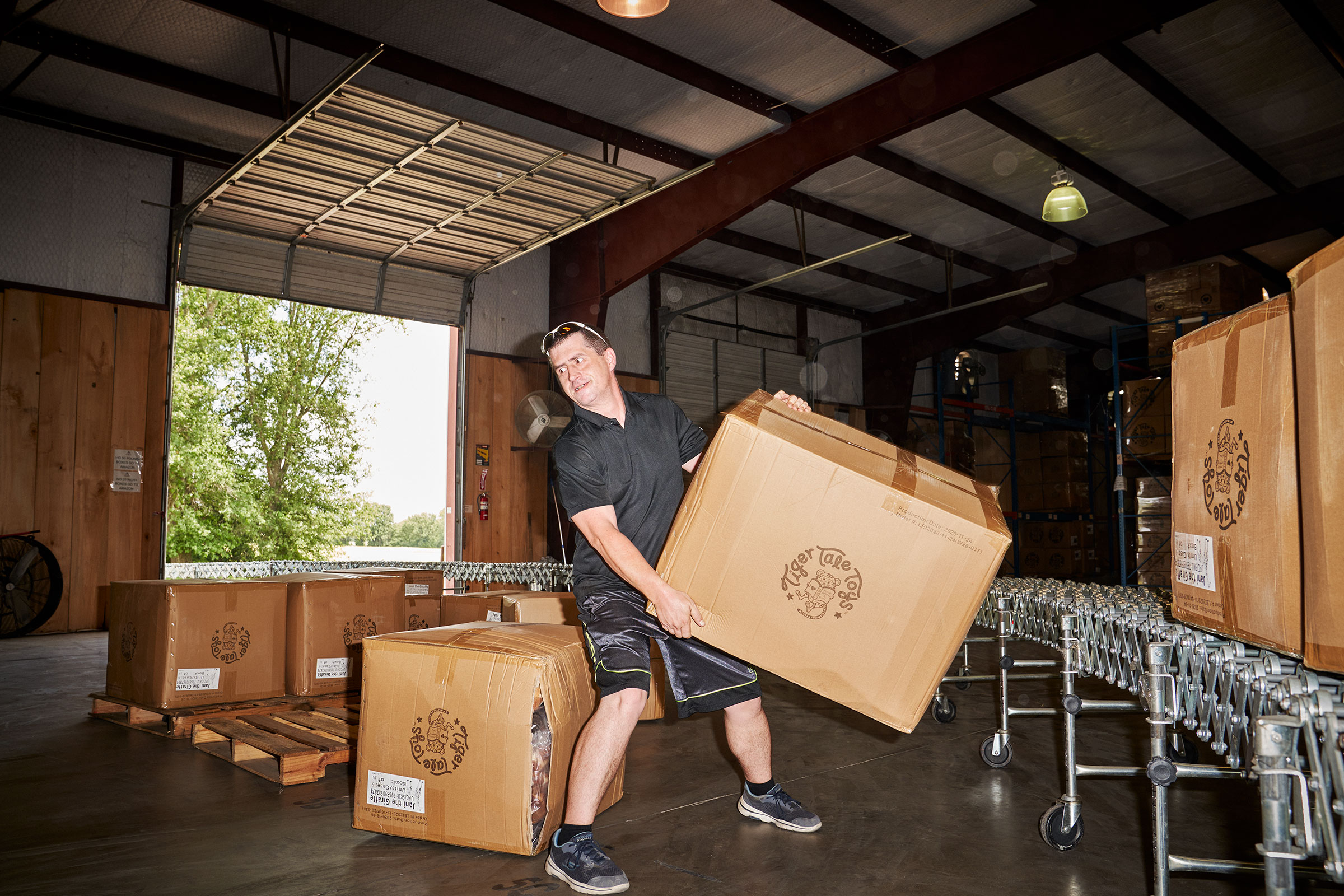
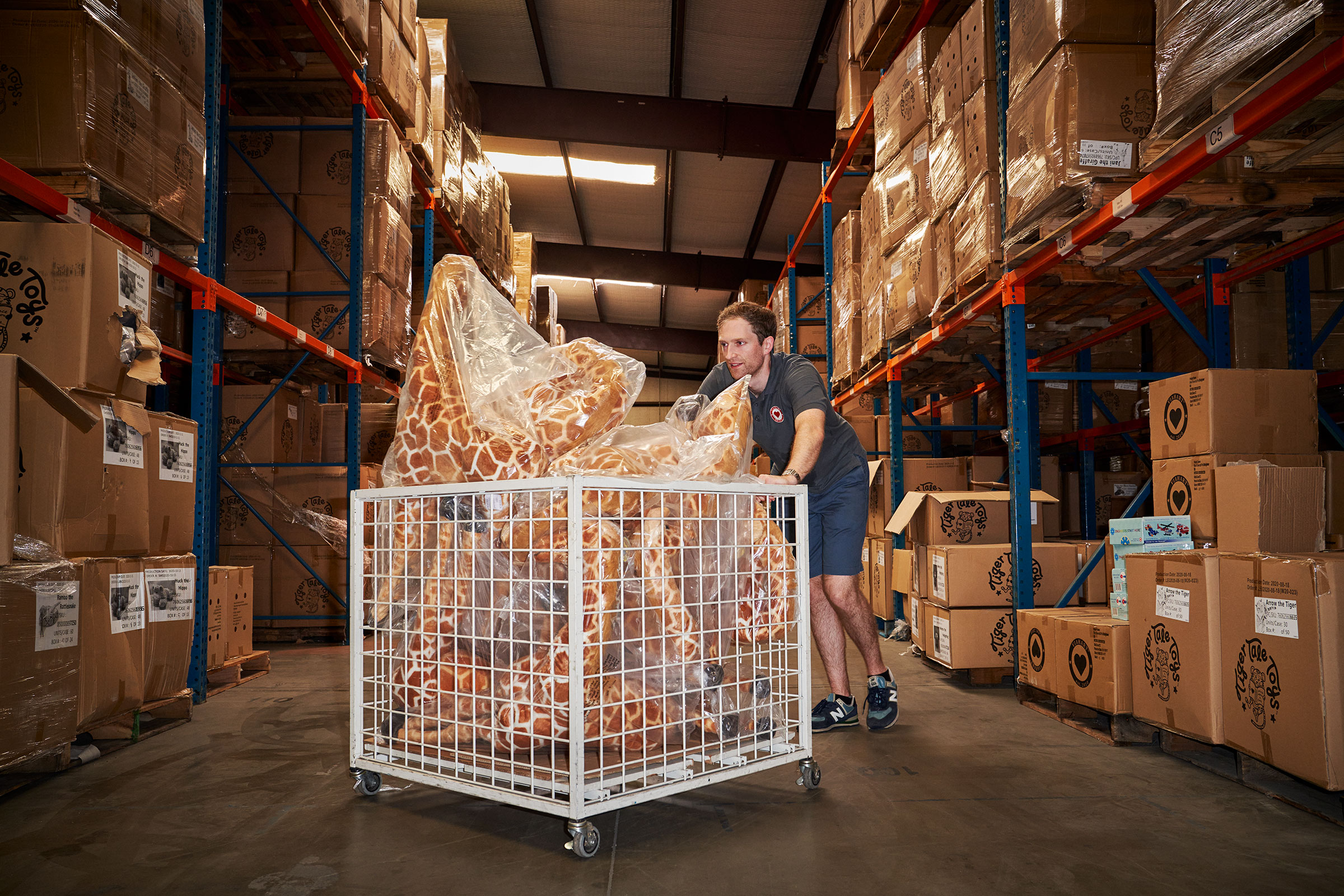
Trucks are an important part of getting containers from the ports to warehouses. They’re also what get packages from those warehouses to the customer’s doorstep. As delays mount at ports and railyards, truck trips are taking longer, since truckers have to sit around waiting.
Some trucking companies allow around two hours of free waiting time, and then start charging logistics companies for any extra time that the driver waits. Since there is so much demand, trucking companies are running on a tight schedule—if a truck breaks, or a container gets delayed, or a warehouse is short-staffed, it throws off future deliveries, too. “There’s no room for mistakes at all,” says Ramirez, the terminal operator.
The trucking industry’s labor problems
Though the trucking industry frequently complains of labor shortages, there’s been a very fragile supply chain in many parts of the trucking industry since it was deregulated in the 1980s, says Steve Viscelli, a sociologist at the University of Pennsylvania and the author of Big Rig: Trucking and the Decline of the American Dream. Now, hundreds of thousands of drivers pay their own expenses and don’t make any money when there isn’t cargo being moved, which means that in the beginning of the pandemic, when there wasn’t any cargo being moved because factories in China had closed, lots of truckers had to look for other ways to make money.
Jobs hauling containers to and from ports, and those taking containers long-distance—so-called over-the-road drivers—are some of the worst jobs in trucking, Viscelli says. Since deregulation, many of these truckers are now independent contractors who get paid by the load. That means the delays at ports and terminals hit them particularly hard. They’re deciding it’s not worth the money if they’re just going to sit around waiting for hours, and not getting paid for that time. The average annual turnover rate for long-haul truckers at big companies was more than 90% before the pandemic, and probably has gone up since then. Companies like Walmart are offering big signing bonuses to try to increase retention as demand surges.
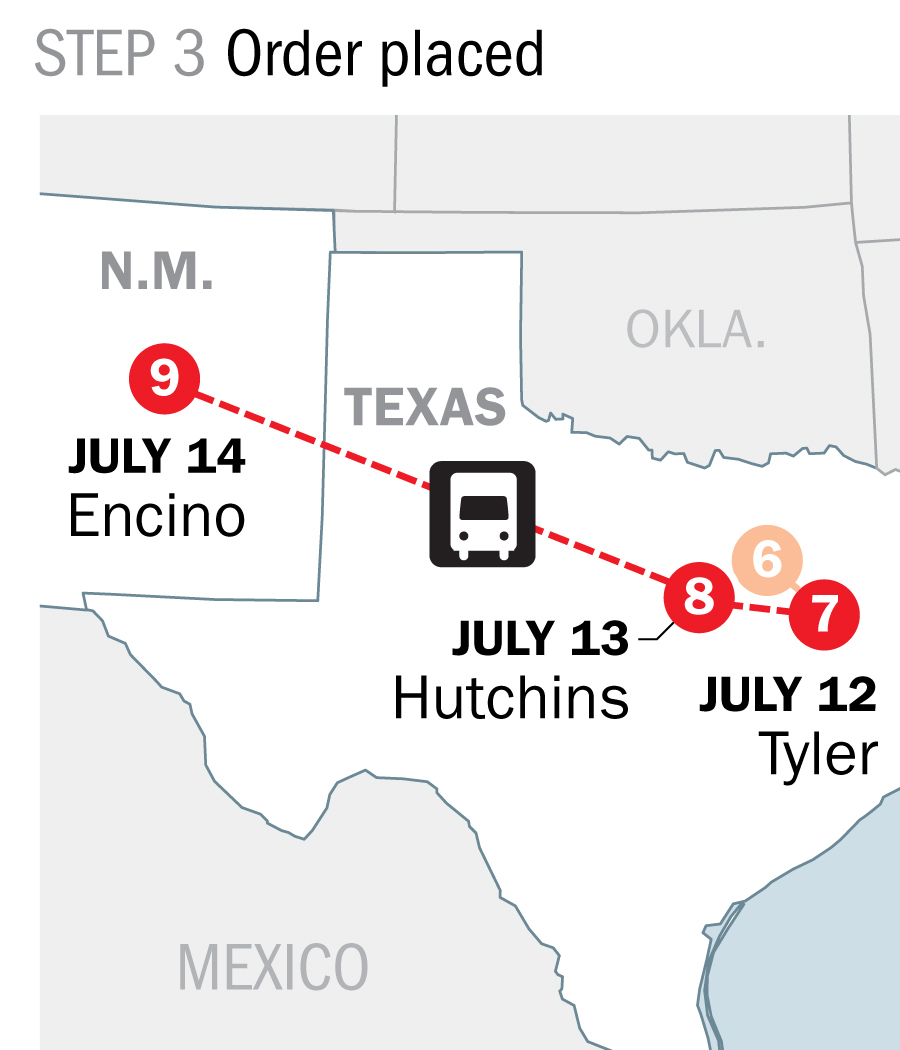
Many other pieces of getting Jani from the warehouse to my doorstep got more expensive, too. Before the pandemic, Viahart paid entry level workers at its Texas warehouse $10-11 an hour. Then, this spring, he started having trouble finding people. He raised the wage to around $14-15 an hour, which helped him hire enough people to keep the warehouse running, but also increased the cost of getting Jani to my doorstep.
Labor wasn’t the only cost that went up in the warehouse. The price of boxes went up to $2.17 from $2.03, the result of rising cardboard prices because of the e-commerce surge. FedEx home delivery shipping, which Hart says is the most economical way for him to get toys to homes, went up 5% this year—the company said in a statement that it has seen more packages entering its network than ever before.
Then, of course, there’s Amazon. Hart tries to sell stuffed animals and toys on his company’s website, but products move much faster when they’re listed on Amazon. More than 90% of his revenues come from toys he’s sold on Amazon, but it, too, is costing him more post-pandemic.
Amazon takes a 15% commission of every item he sells, even the ones like Jani, that Viahart ships itself rather than sending to an Amazon warehouse (Amazon charges for storage space, so it doesn’t make sense for Viahart to send such a big box to Amazon’s distribution centers.) That means as Jani gets more expensive, Amazon takes more money, which in turn makes Jani even more expensive, since Hart has to add on those costs to make a profit. Before the pandemic, Amazon’s commission was around $12. Now, it’s $16.19.
Doorstep delivery
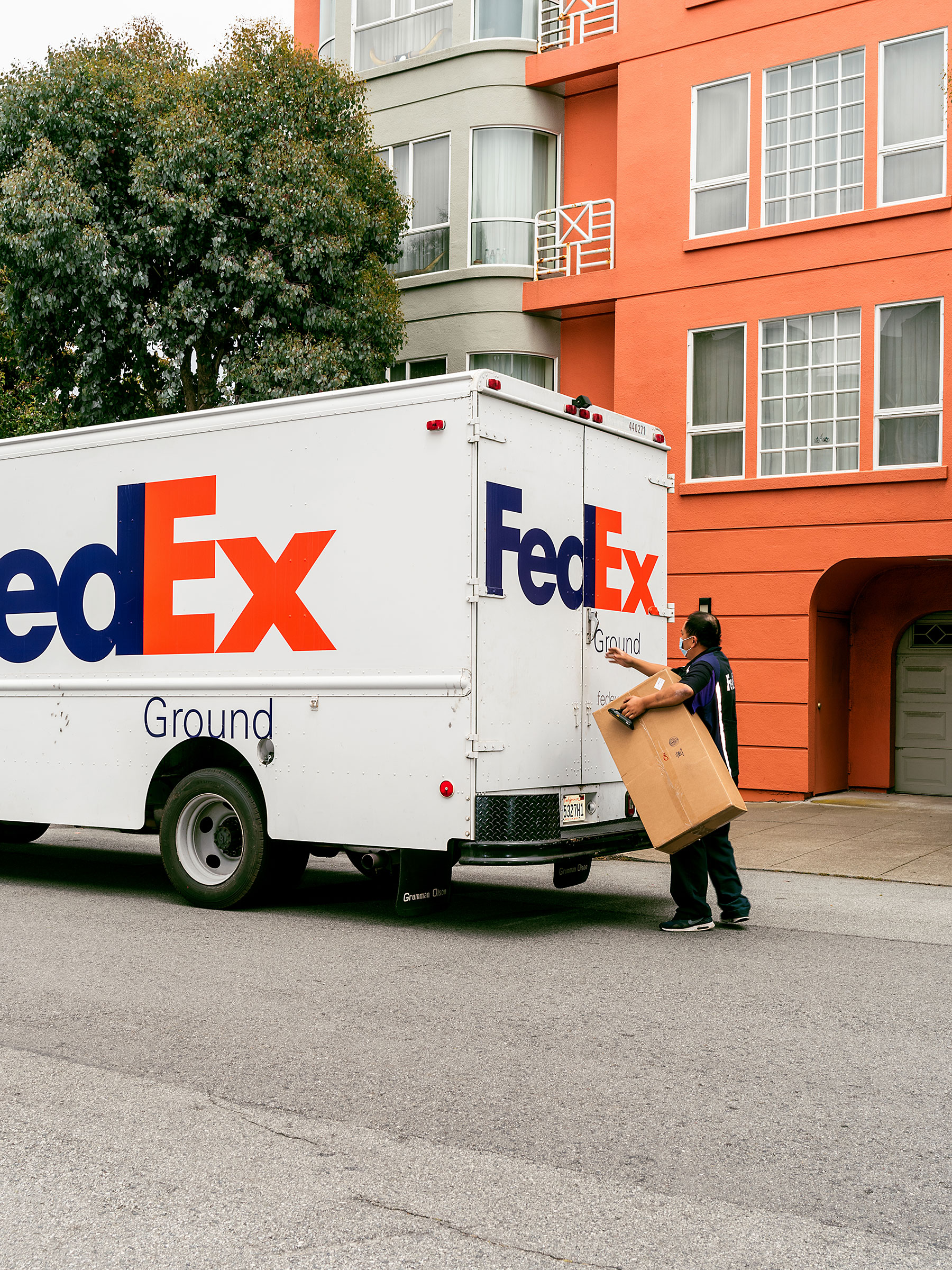
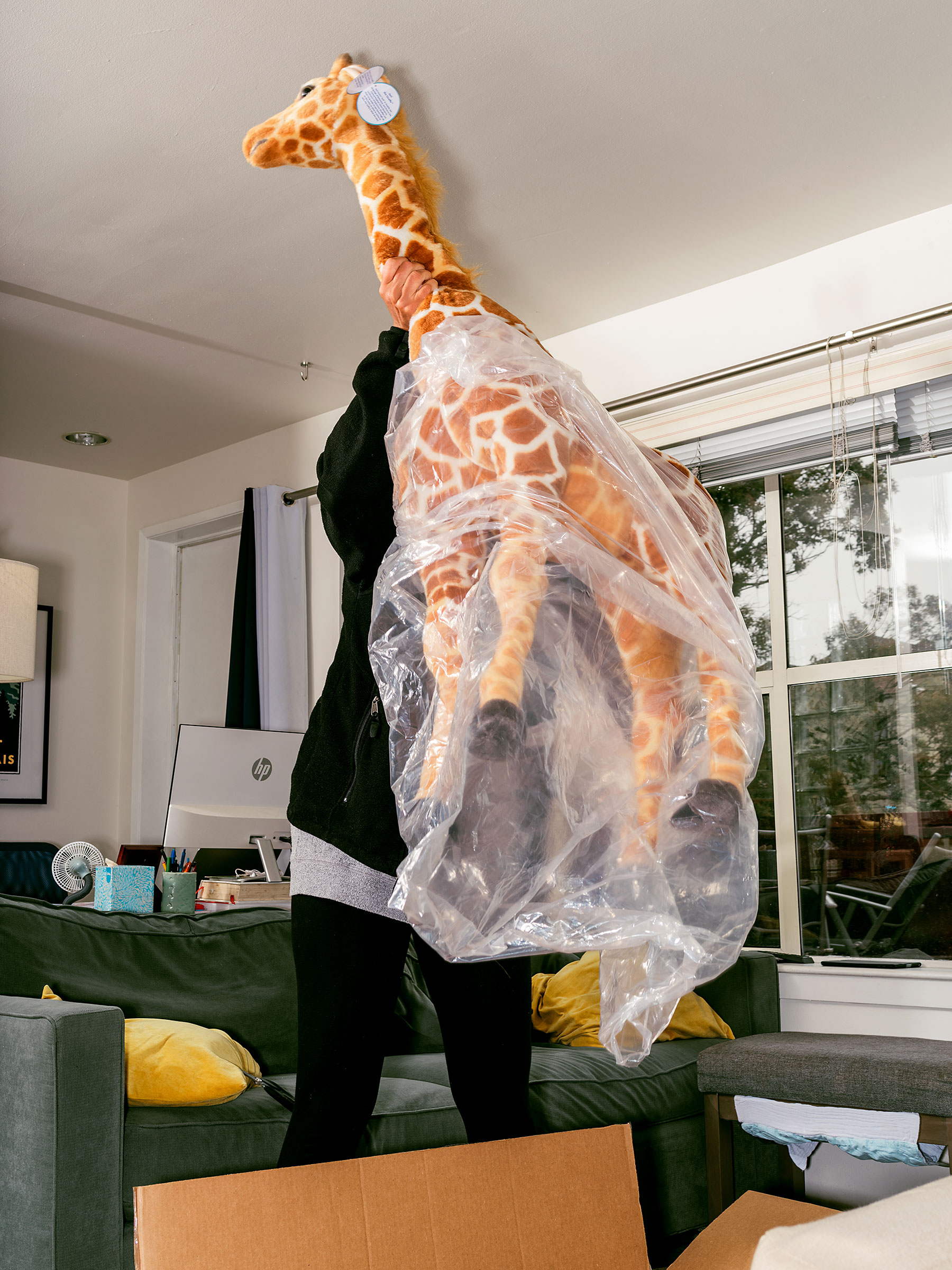
I ordered Jani on July 12, about seven months after she’d been unloaded in the warehouse. Thanks to updates from FedEx, I could track her journey by truck, from Hart’s warehouse to Tyler, Texas, to Hutchins, Texas, then overland to Encino, N.M., right in the center of the state, where she arrived at 7:20 p.m. on July 14. By the next morning at 6:22 a.m., she was in Essex, Calif., right on the border with Arizona; by 9:21 p.m. that day, she was in Tracy, a logistics hub outside of San Francisco. She got to South San Francisco by 4:18 in the morning on July 16, and then ended up on my doorstep in San Francisco at 2:07 p.m.
A very nice FedEx driver named Jemy Balicanta brought her into my apartment building and to my front door, looking a little confused as to why I seemed so awed by the fact that this package had arrived. I kept thinking of the dozens of stops Jani had made along the way, like a pinball bouncing around a crowded machine so much longer than you’d first expect. Before the pandemic, Jani could have gotten from the factory to my doorstep in about 81 days; now it takes 106 days, or, in my case, longer.

If I was awed, Mike Molson Hart was stressed. He’d hoped that Jani would come in before the Christmas rush last year, and anticipated that he’d sell out of plush toys like her. Instead she arrived long after people had completed their holiday shopping. This uncertainty and risk is one more reason prices are going up, he says. If he expected to have 3,000 units in stock for the holiday season, but only got 1,000, he has to raise prices to compensate for the delayed stock, and so he can pay his bills. “That’s what’s happening everywhere,” he says. When there’s more demand than there is supply, businesses can charge more.
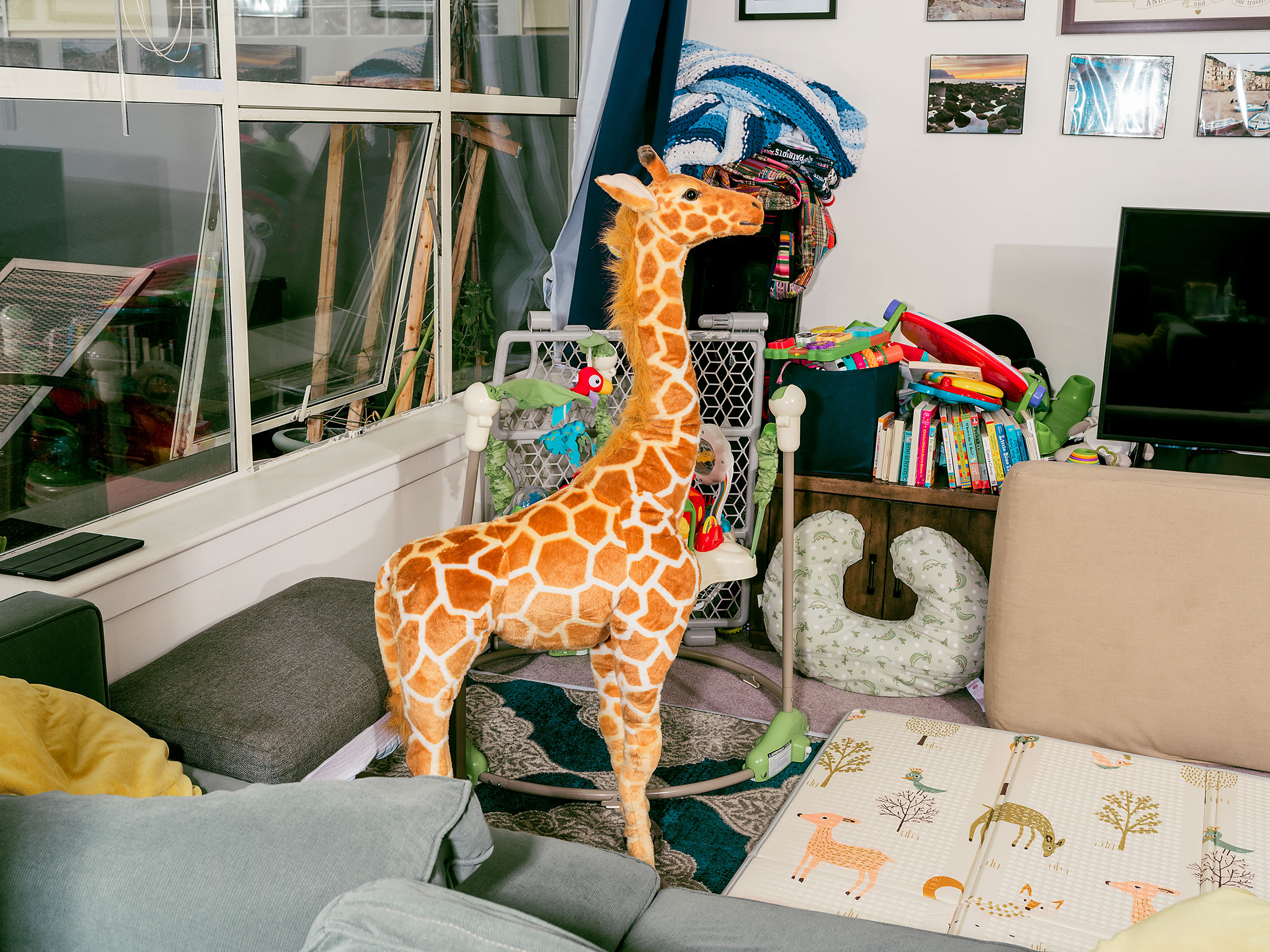
When we spoke, Jani’s price still wasn’t listed above $100 on Amazon, and I asked Hart why. The toy company Melissa and Doug sells a similar giraffe, he says. If Hart raises his prices on Amazon and his competitors don’t, consumers won’t buy from him. But as we talked, he noticed that Melissa and Doug’s giraffe was listed as Out of Stock—probably because of some of the supply chain snafus Jani had experienced. “Well maybe we can raise the price,” he said.
Jani is standing in my living room, alongside my son’s bright plastic piano and stuffed animals and plastic laptop and all sorts of other brightly-colored toys that I’m pretty sure also came all the way from China. It’s a little depressing to think of all the energy that was expended to get those toys across the sea, through the ports, on the railways, and in a truck, to my doorstep. If prices for all those cheap Chinese toys go up, I can’t really be upset. A journey that is that much of a headache should cost something, after all.
More Must-Reads from TIME
- Cybersecurity Experts Are Sounding the Alarm on DOGE
- Meet the 2025 Women of the Year
- The Harsh Truth About Disability Inclusion
- Why Do More Young Adults Have Cancer?
- Colman Domingo Leads With Radical Love
- How to Get Better at Doing Things Alone
- Michelle Zauner Stares Down the Darkness
Contact us at letters@time.com