
It was 11:00 in the morning on Oct. 28, 1965—exactly 50 years ago—when the final metal section of the St. Louis’ Gateway Arch was put into place, completing a monument decades in the making. It was a moment of pride for those who worked on the project, as well as vindication.
During the years of construction on the 630-ft. arch, it wasn’t a given that the two sides ever would meet in the middle. Engineers and builders had to trust that their calculations and construction were accurate, knowing that if the angle of either side was even a little bit off, the moment of triumph would instead be a moment of disaster.
“There were quite a few people over the years who had thoughts that it never would [meet at the top],” recalls Ken Kolkmeier, who was the project manager for the fabrication and construction of the Arch. “I don’t think anybody in our organization ever felt that it wouldn’t meet.”
Those who built the arch were just as proud of another accomplishment. The insurance company for the project had projected that up to 13 men would die during the process due to accidents—they were, after all, working hundreds of feet in the air with no nets—but not a single worker did. In fact, Kolkmeier says the crew went 500 days without a lost time accident.
Still, Kolkmeier says that it was a difficult project that required the best welders and iron workers available. The construction of the arch was a complicated process. Individual sections were made in Warren, Penn., and brought by railroad to St. Louis. Each section contained a piece of corner, so that the overall shape was something like a “7,” says Bob Moore, a historian with the National Park Service. Doing it that way meant that the builders on site would be able to assemble the pieces without calculating tricky angles.
The curve of the monument—a shape known as a catenary arch—was calculated by hand, with the Army Corps of Engineers using a calculating device (“what we would not even consider to be a computer today,” Moore jokes) to double-check the precision. Builders could only take measurements at night, since warm sunlight caused the structure to flex very slightly. Constant measuring and adjusting kept the arch on track. “They’d prop each piece up with wood until they were sure it was totally right,” Moore says, “then remove the wood and the welders would come in.”
The multi-step manufacturing process meant not everyone who worked on the project got to see the building as it progressed. Ike Erdman, a then-27-year-old welder who worked in the Warren factory, says he never got to visit the site. Another welder didn’t even know what they were working on. “Some guy said, ‘What are we building here? What is this thing anyway?'” Erdman recalls. “And another guy said, ‘Well, it’s an arch. It’s going out to St. Louis. It’s gonna be the Gateway to the West.’ The fellow standing next to me says, ‘What do they need a gateway to the west for? They’ve been going out there for 200 years.'”
It was years before Erdman finally visited the arch in person, but the sense of pride he got from it was enough that he plans to be back for the anniversary celebration on Wednesday.
“It gives you this feeling like, did I really work on this?” he says. “I get to thinking about the men I worked with in Warren. They were good workers and worked hard. Nobody else ever built one of these and nobody else probably ever will build another one. And to think you were a part of that—it’s an honorable thing.”
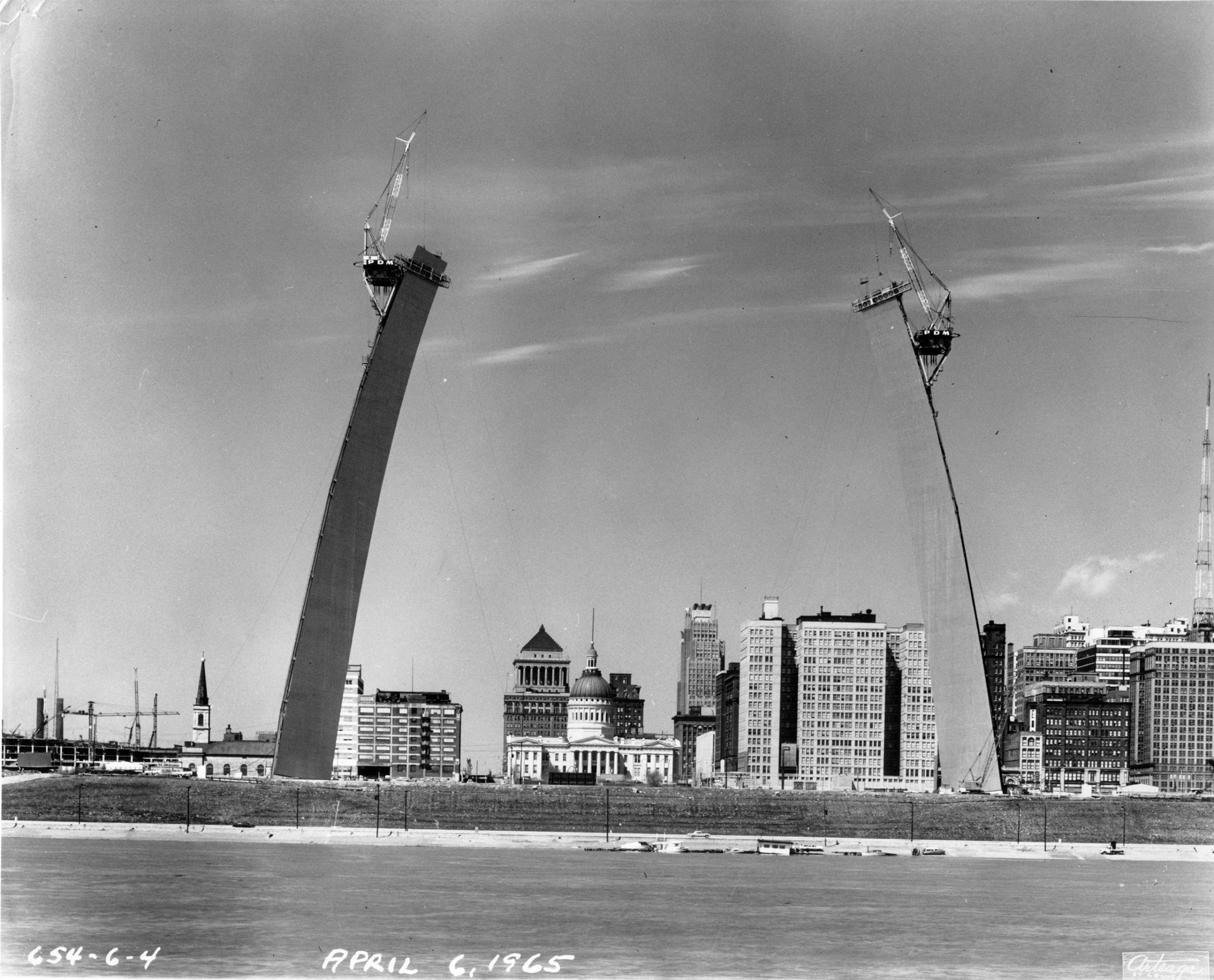
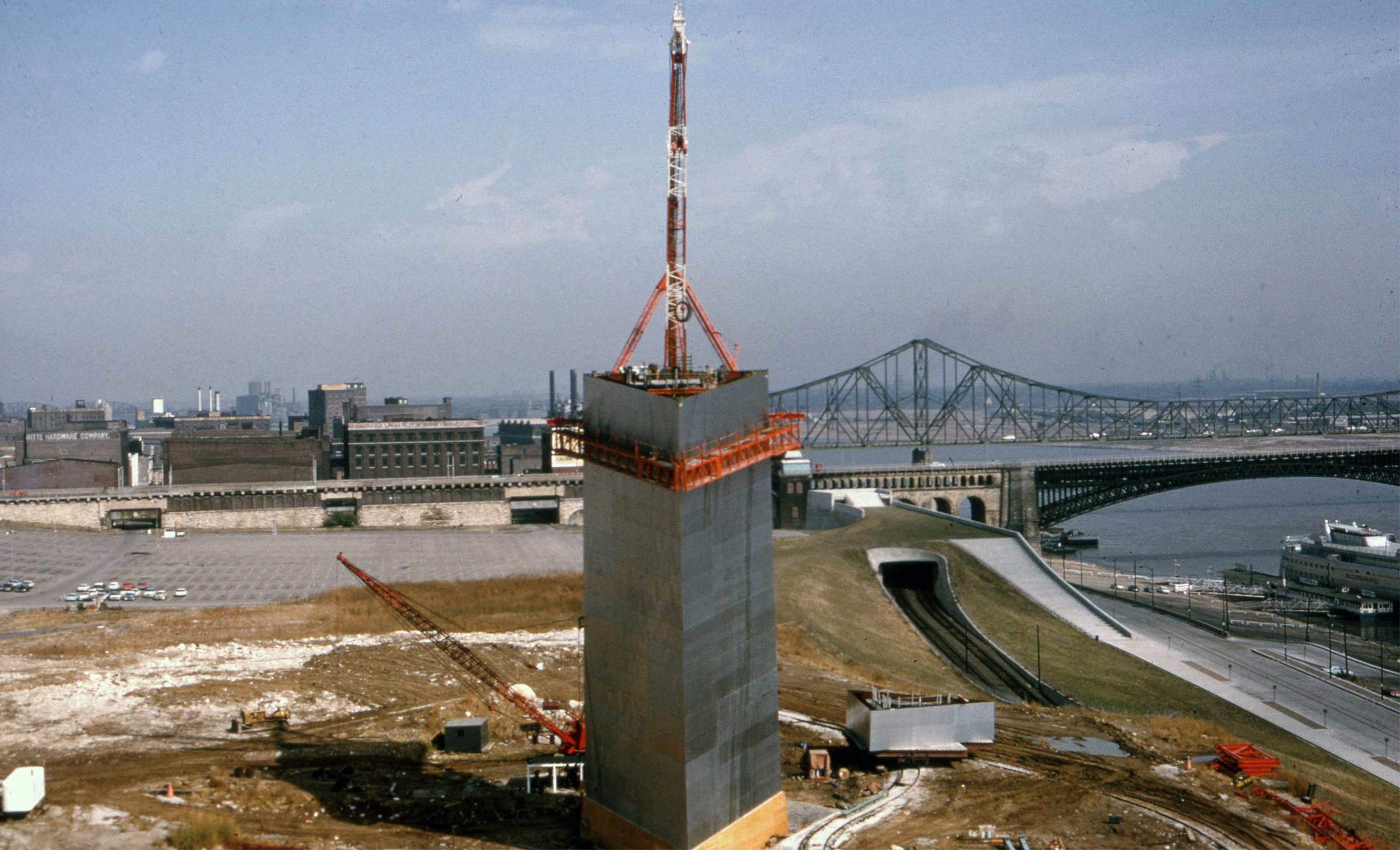
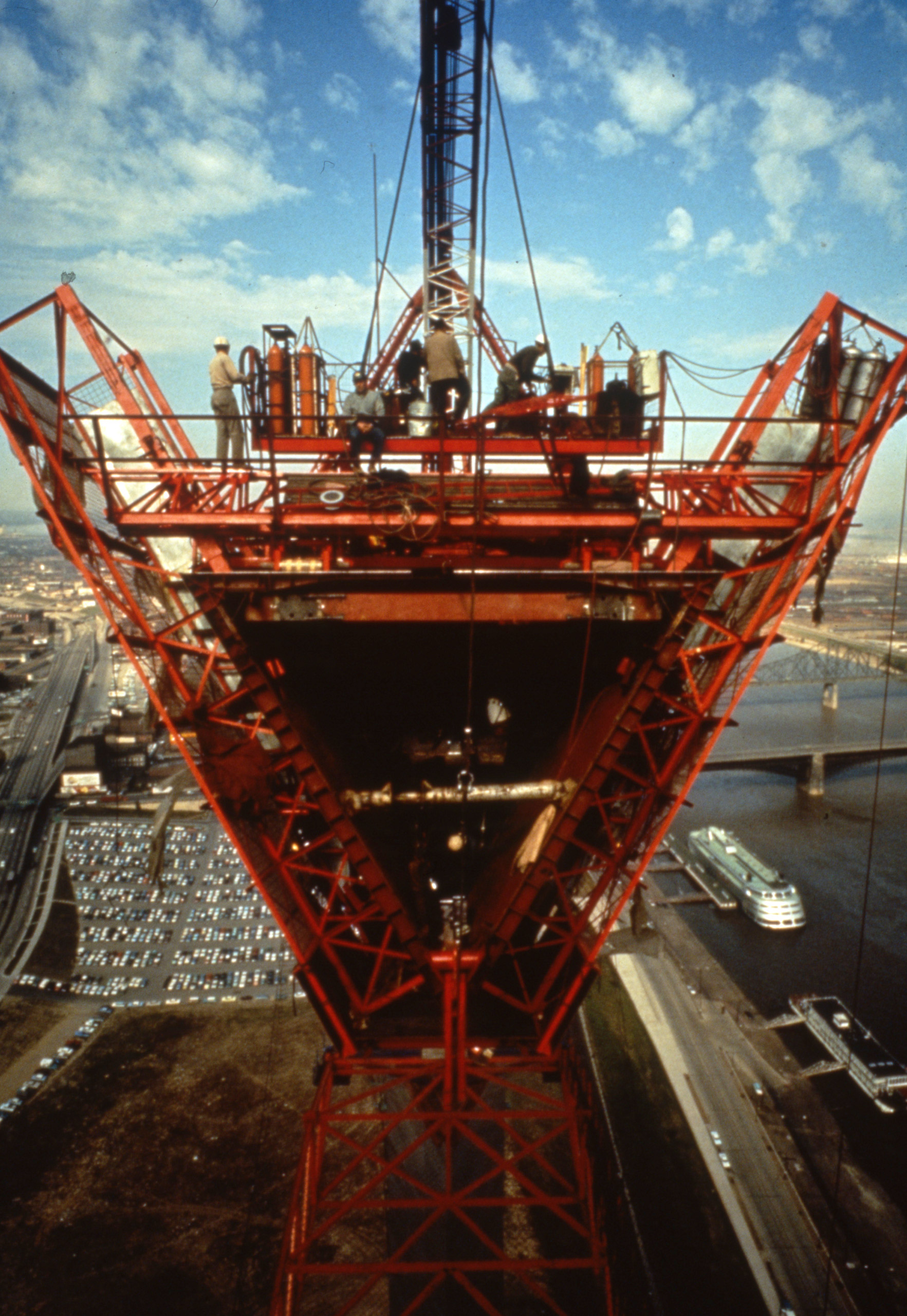
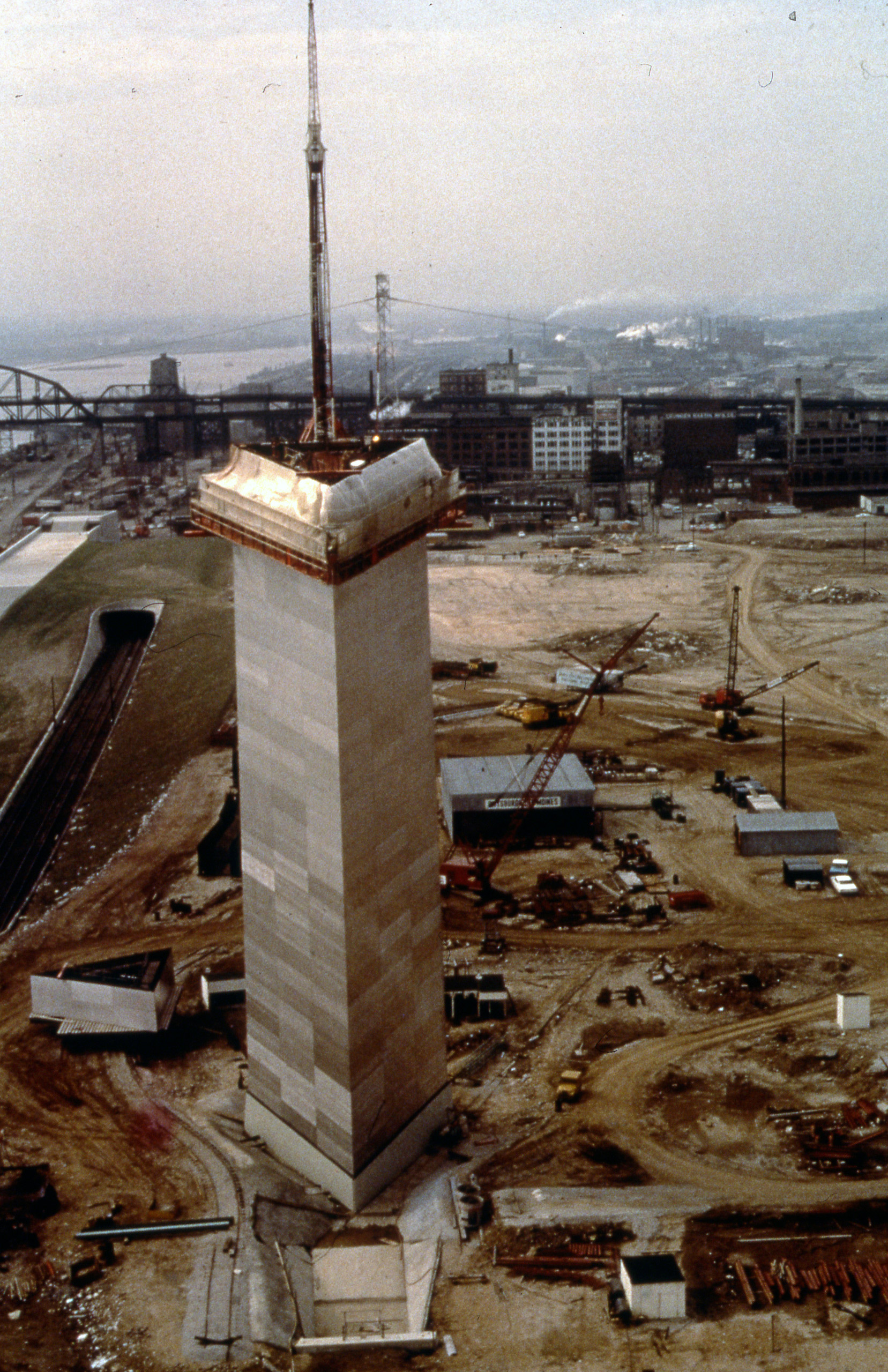
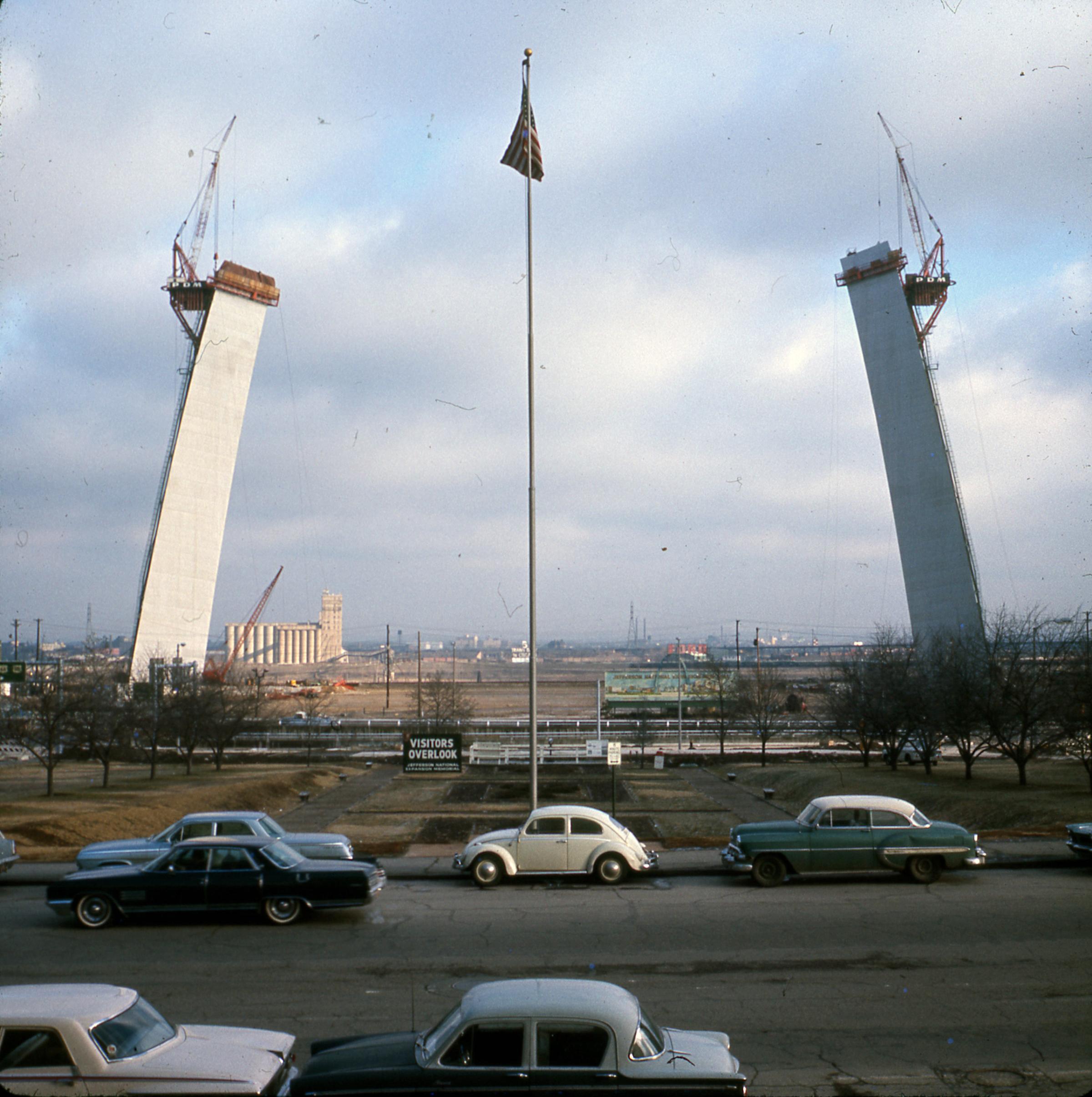
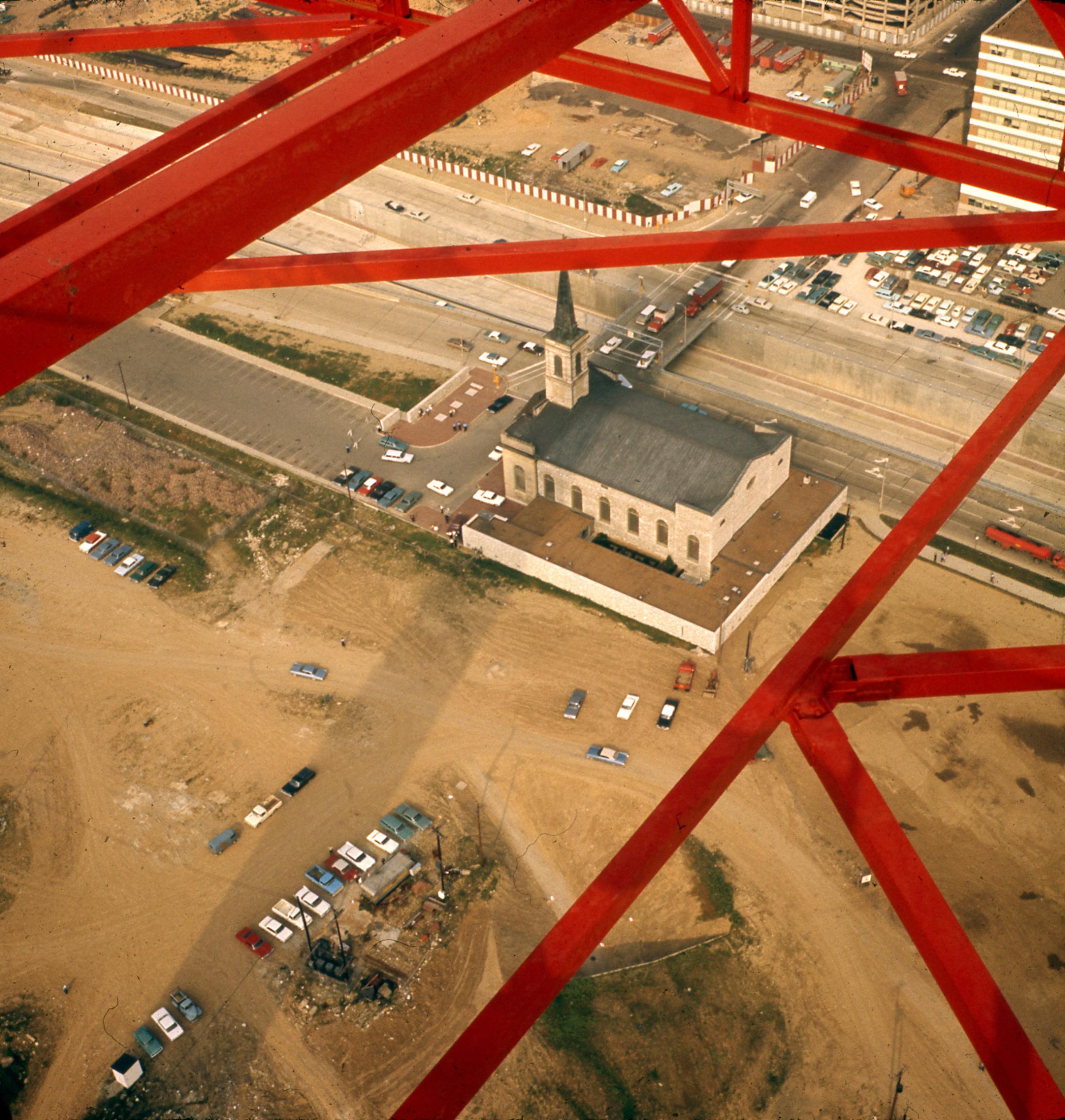
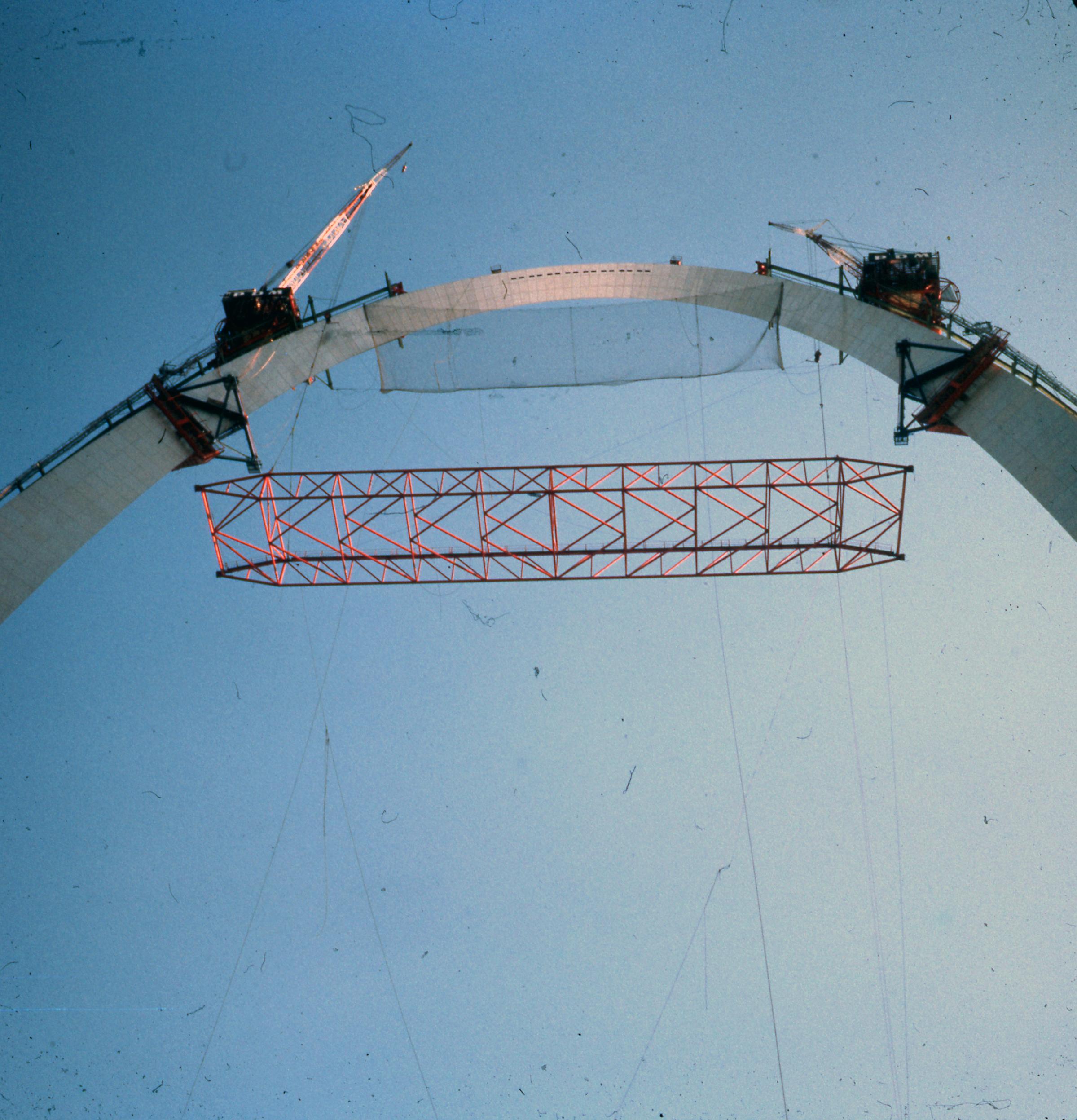


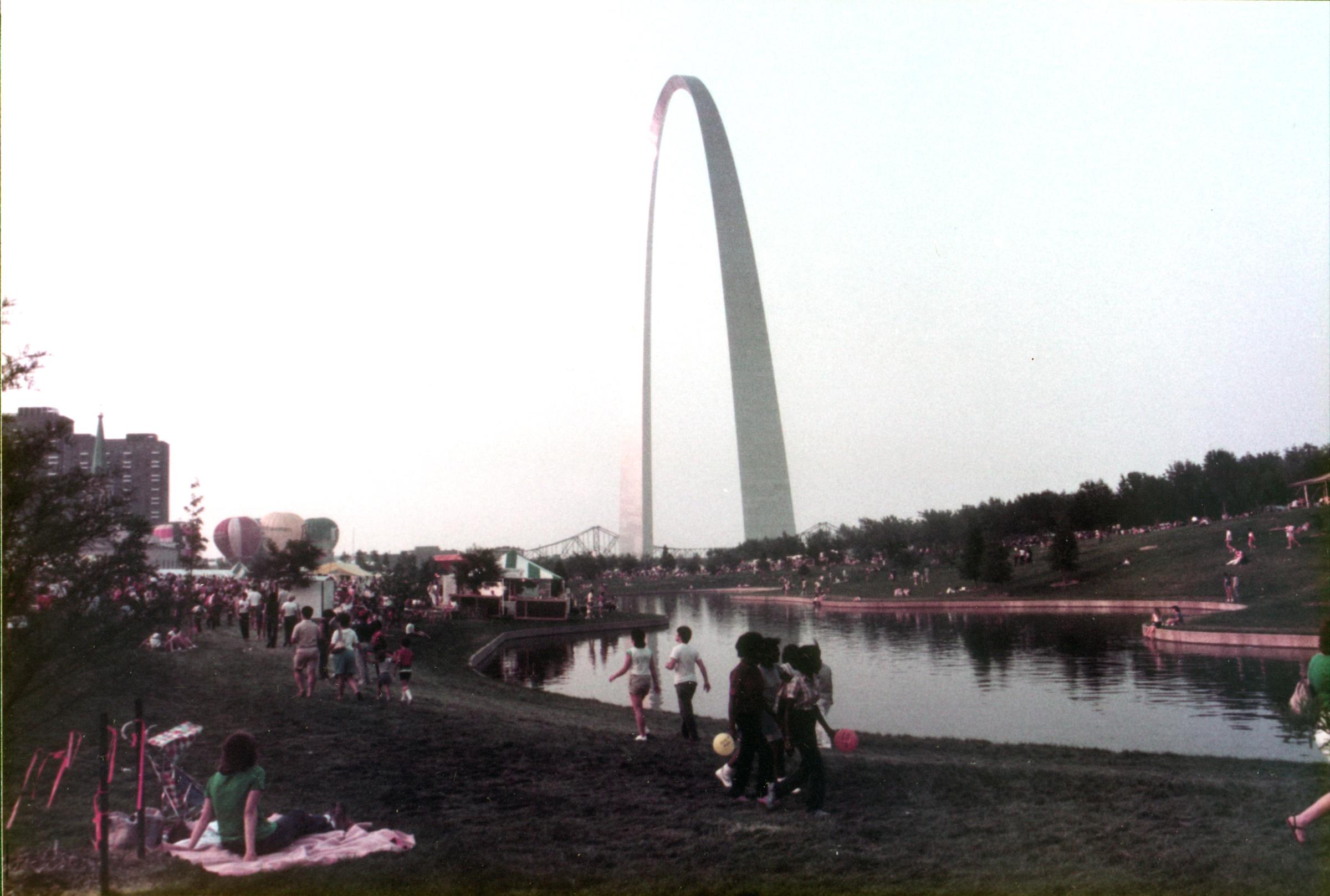
More Must-Reads from TIME
- Cybersecurity Experts Are Sounding the Alarm on DOGE
- Meet the 2025 Women of the Year
- The Harsh Truth About Disability Inclusion
- Why Do More Young Adults Have Cancer?
- Colman Domingo Leads With Radical Love
- How to Get Better at Doing Things Alone
- Michelle Zauner Stares Down the Darkness
Write to Lily Rothman at lily.rothman@time.com